Resumen
- Alfa Project, una empresa con sede en Polonia, reproduce piezas dañadas o no disponibles para coches antiguos mediante ingeniería inversa.
- Ellos modelan en 3D cada parte en un software CAD y usan su Zortrax M300 Plus para entregar los productos solicitados.
- La impresión 3D demostró ser un método de producción rentable y confiable en la industria automotriz.
La industria automotriz ha estado aprovechando las tecnologías de fabricación aditiva durante muchos años. La impresión 3D agiliza los procesos de diseño y construcción de automóviles, brindando a los fabricantes más libertad de diseño y posibilidades eficientes de creación de prototipos. Pero en algunos casos, las impresoras 3D se utilizan en el sector de la automoción de una forma ligeramente diferente. Aquí hay un ejemplo de una empresa que modela en 3D y reproduce partes rotas o no disponibles de vehículos y usa una impresora 3D Zortrax para ese propósito.
Impresión 3D en ingeniería inversa: de proyectos CAD a piezas funcionales
Impresión 3D en ingeniería inversa: de proyectos CAD a piezas funcionales
Alfa Project es una empresa polaca propiedad de los hermanos Mateusz y Przemysław Dziwisz, quienes tienen un gran interés en la motorización italiana, particularmente en los automóviles fabricados por Alfa Romeo. Habiendo utilizado los autos de esta marca durante muchos años, decidieron comprar el clásico Alfa Romeo Spider de 1988. Tal como habían pronosticado, el interior del auto presentaba considerables signos de desgaste: “Muchos elementos de plástico estaban dañados. Las piezas de repuesto disponibles en el mercado eran muy caras y todavía tenían defectos. Incluso cuando encontramos algunos artículos bien conservados, sabíamos que el plástico utilizado para producirlos se volvió muy frágil después de tantos años”. – señala Mateusz.
Alfa Project es una empresa polaca propiedad de los hermanos Mateusz y Przemysław Dziwisz, quienes tienen un gran interés en la motorización italiana, particularmente en los automóviles fabricados por Alfa Romeo. Habiendo utilizado los autos de esta marca durante muchos años, decidieron comprar el clásico Alfa Romeo Spider de 1988. Tal como habían pronosticado, el interior del auto presentaba considerables signos de desgaste: “Muchos elementos de plástico estaban dañados. Las piezas de repuesto disponibles en el mercado eran muy caras y todavía tenían defectos. Incluso cuando encontramos algunos artículos bien conservados, sabíamos que el plástico utilizado para producirlos se volvió muy frágil después de tantos años”. – señala Mateusz.

Alfa Romeo Spider, propiedad de Mateusz y Przemysław del Proyecto Alfa.
Mateusz y Przemysław optaron por reproducir esas partes dañadas por su cuenta. Optaron por el modelado 3D y por tener las piezas impresas en 3D por contratistas externos. Después de eso, mostrar los efectos de su trabajo entre otros entusiastas de los autos antiguos les hizo darse cuenta de que había una demanda creciente para crear artículos para el interior de los autos que ya no estaban disponibles comercialmente. Por eso compraron su primera impresora 3D FDM, Zortrax M300 Plus, y decidieron seguir desarrollando su proyecto y trabajar en piezas para otros propietarios de automóviles.
Los pedidos que comenzaron a recibir muy a menudo involucraban elementos que estaban demasiado deformados para ser escaneados en 3D. Entonces, el equipo del Proyecto Alfa se dio cuenta de que la única forma en que podían recrear una pieza determinada era diseñarla manualmente desde cero. Por lo tanto, comenzaron a seguir el proceso llamado ingeniería inversa y usar su impresora 3D de escritorio para crear prototipos y, a veces, incluso producir el elemento final. ¿Cómo suelen empezar sus proyectos? Primero, descomponen cada parte en sus componentes separados para recopilar los datos necesarios para el modelo 3D en el software CAD. El resto del trabajo se lleva a cabo internamente: “La impresión 3D es una herramienta que nos permite transferir fácilmente un proyecto directamente del programa CAD a la realidad. Esto hace que sea mucho más fácil trabajar en ingeniería inversa para la industria automotriz”. – dice Mateusz.
Los pedidos que comenzaron a recibir muy a menudo involucraban elementos que estaban demasiado deformados para ser escaneados en 3D. Entonces, el equipo del Proyecto Alfa se dio cuenta de que la única forma en que podían recrear una pieza determinada era diseñarla manualmente desde cero. Por lo tanto, comenzaron a seguir el proceso llamado ingeniería inversa y usar su impresora 3D de escritorio para crear prototipos y, a veces, incluso producir el elemento final. ¿Cómo suelen empezar sus proyectos? Primero, descomponen cada parte en sus componentes separados para recopilar los datos necesarios para el modelo 3D en el software CAD. El resto del trabajo se lleva a cabo internamente: “La impresión 3D es una herramienta que nos permite transferir fácilmente un proyecto directamente del programa CAD a la realidad. Esto hace que sea mucho más fácil trabajar en ingeniería inversa para la industria automotriz”. – dice Mateusz.

Impresión 3D realizada por Alfa Project en su Zortrax M300 Plus.
Perfeccionamiento de las piezas finales con prototipos rápidos
Mateusz y Przemysław realmente se preocupan por ofrecer productos confiables que puedan sustituir a los instalados en los automóviles y mantener las mismas funcionalidades. Modelan y reproducen en 3D spoilers, parachoques, perillas de cambios, cubiertas de mecanismos de caja de cambios, soportes de espejos y múltiples elementos del tablero, como marcos de relojes, salidas de aire, paneles de control de CA o placas ciegas. Pero debido a que las piezas originales son susceptibles de dañarse con el uso regular, el equipo se enfoca en mejorar el diseño de cada pieza: “Al diseñar una pieza, agregamos características, como nervaduras, que fortalecen el artículo final, especialmente en lugares particularmente sujetos a daños o donde se dañó el elemento original.” – explica Przemysław.
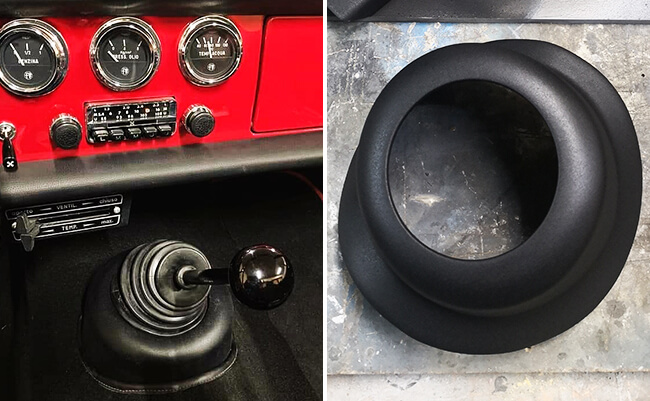
Una cubierta del mecanismo de la caja de cambios impresa en 3D y posprocesada por Alfa Project para uno de sus clientes que también posee un Alfa Romeo Spider.
Después del modelado 3D inicial, el equipo pasa a la impresión 3D de un prototipo. A continuación, la pieza impresa se compara con la original y se ajusta al lugar donde finalmente se asentará. De esta forma, el equipo de Proyecto Alfa comprueba si la pieza cumple con los criterios dimensionales y geométricos. Según destacan, Zortrax M300 Plus es una herramienta imprescindible para esta etapa de su trabajo: “Gracias al prototipado rápido, podemos aplicar cambios al proyecto de forma rápida y sencilla y crear elementos en menos tiempo. Al mismo tiempo, podemos mejorar significativamente el ajuste de los elementos impresos al equipo ya existente”. Una vez que se acepta el prototipo, Mateusz y Przemysław continúan produciendo la pieza final. Dado que suelen fabricar piezas únicas, Zortrax M300 Plus se ha convertido en la principal máquina de producción de su taller, lo que garantiza rentabilidad frente a otros métodos, como el fresado o el moldeado.

Salida de aire Alfa Romeo Spider impresa en 3D instalada en el salpicadero (a la izquierda). Una salida de aire original comparada con las salidas de aire reproducidas por Alfa Project (a la derecha).
Modelos impresos en 3D como sustitutos de piezas de fábrica
El equipo del Proyecto Alfa evalúa cada proyecto individualmente en términos del entorno, las condiciones y las fuerzas que afectarán al elemento producido. Esto les ayuda a configurar correctamente la geometría durante la impresión 3D para que la pieza lista esté sujeta a las fuerzas de flexión, en lugar de las de corte que debilitarían el modelo. En sus proyectos, Mateusz y Przemysław eligen uno de los filamentos más populares utilizados en el sector automotriz: Z-ABS.
Modelos impresos en 3D como sustitutos de piezas de fábrica
Según afirman, el filamento correctamente seleccionado les permite crear elementos tan duraderos como las piezas de fábrica: “En los elementos de plástico impreso, el Z-ABS otorga una resistencia a la temperatura satisfactoria, y al mismo tiempo es adecuadamente resistente a la flexión. Se puede utilizar en modelos 3D con sujetadores o elementos de anclaje”. Finalmente, las impresiones 3D se pulen y barnizan para que coincidan lo más posible con la pieza original.
Lanzar el Proyecto Alfa permitió a Mateusz y Przemysław abordar el problema de la disponibilidad de elementos plásticos en vehículos que han dejado de fabricarse. El uso de la impresora 3D Zortrax M300 Plus en su negocio ahora les ayuda a producir piezas de alta calidad con una gama completa de funcionalidades. De hecho, los productos del Proyecto Alfa han llegado a otros entusiastas de los coches antiguos: “Actualmente, nuestras piezas se utilizan en vehículos de todo el mundo y, lo que es más importante para nosotros, los clientes están satisfechos con nuestro trabajo”. En el futuro, Mateusz y Przemysław planean expandir su oferta introduciendo nuevos tipos de filamentos, especialmente los reforzados con fibra de vidrio y carbono.
Descubra cómo se utilizó Zortrax M300 Plus en otros proyectos: Dancer Bus, ML System.
Descubra cómo se utilizó Zortrax M300 Plus en otros proyectos: Dancer Bus, ML System.